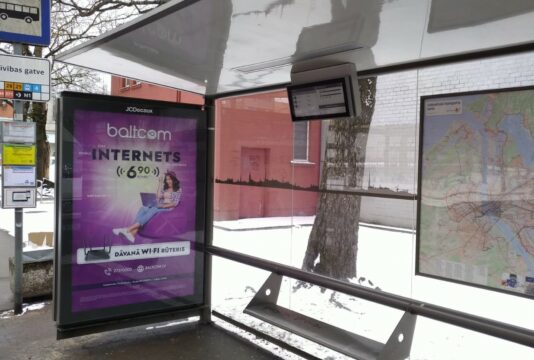
Rīgas Satiksme (Riga municipality public transportation) achieves significant cost and carbon savings with Papercast e-paper
Rīgas Satiksme is further enhancing the travel experience for Riga’s Public transport users with the second…
If you asked us 5 years ago what we would be doing in 5 years’ time – in fact, if you asked us 1 year ago – we still never would have predicted how this last year has played out.
We don’t need to lay out the details, most of us are living with restrictions in one form or another. But one of the most significant – and the most relevant to this article – is the travel restrictions. Not only has this had a direct (and profound) impact on our sector, but it has also changed how we go about our day to day business.
We serve a global customer base from our London head office, with development and manufacturing in Slovenia. It is not uncommon for new customers to visit our production facilities so they can see what goes into creating our innovative e-paper displays.
Restrictions on global travel have put these visits on hold.
We planned to produce a video, but unfortunately, we have not been able to give external visitors access to our production facilities. Our priority is to both keep our team safe and keep production at full capacity.
And so here we are, taking you on a different type of journey. One with a photo story put together by our Production Planning Manager, Nina Čebin. Here she will walk you through the Papercast production process, so you can see what goes into assembling our e-paper displays and solar power modules to the highest standards.
Preparing the front housing frame and installing the speakers
Preparing the back housing frame and installing the connectors
Preparing the display module and installing the LED lights
Glazing the front housing frame
Optical bonding quality control
Installing the display module into the front housing frame
Attaching the display module, sealing the frame with silicone tube and glass with silicone glue
Installing the electronics, and connecting the cables and processing boards
Scanning serial numbers, control procedure, installation of test SIM and SD cards
24h burn-in test
Removing the test SIM card, securing the back housing to complete the display, detailed cleaning and applying the protective screen foil, generating QA report
Packing
Assembling the solar panel onto the solar frame
Installing the BMS processing board on the BMS holder
Connecting the battery box with the solar frame and panel
Testing
Ready to go
We hope you have enjoyed this guided tour through our manufacturing environment. Now you can see what it takes to produce Papercast’s market leading e-paper displays and solar modules. If you have any questions or would like to see our e-paper displays in action, please contact us or book a demo.
Rīgas Satiksme is further enhancing the travel experience for Riga’s Public transport users with the second…
Papercast’s solar and battery-powered e-paper displays are built to last, even in the harshest of…